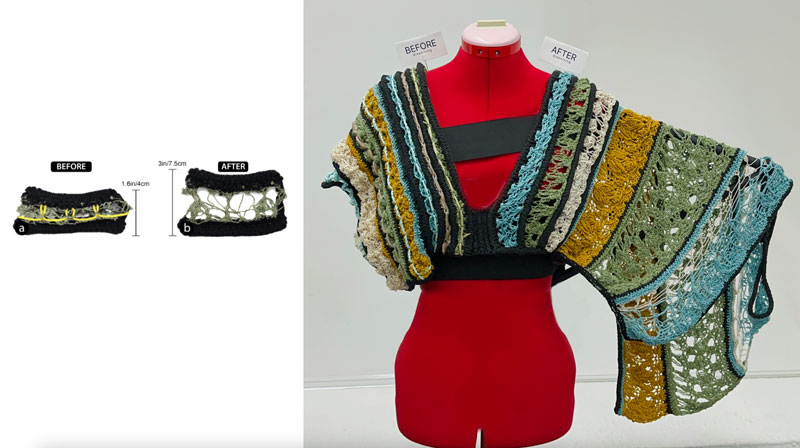
Bio-based materials facilitate the development of more sustainable devices and wearables, expanding the range of design possibilities beyond conventional materials. Our work with biofoam explores one such quality, dissolving, as a unique affordance for designing and interacting with wearables. We developed techniques to make biofoam yarns, and used them to craft three wearables: “Seasonal Footwear”, a “Reveal Bralette”, and an “Unfolding Lace Top”. These wearables incorporate sections that dissolve in water, allowing customization to suit the user’s needs. These wearables illustrate short-term use cases, such as a one-time reveal or shape change. We explore this novel design space as sustainable ephemeral fashion, where bio-based dissolving materials enable revealing, transformative, and interactive functionalities.
Citation: Eldy S. Lazaro Vasquez, Lily M Gabriel, Mikhaila Friske, Shanel Wu, Sasha De Koninck, Laura Devendorf, and Mirela Alistar. 2023. Designing Dissolving Wearables. In Adjunct Proceedings of the 2023 ACM International Joint Conference on Pervasive and Ubiquitous Computing & the 2023 ACM International Symposium on Wearable Computing (UbiComp/ISWC ’23 Adjunct). Association for Computing Machinery, New York, NY, USA, 286–290. https://doi-org.colorado.idm.oclc.org/10.1145/3594739.3610781
Video: https://youtu.be/jbCfofXDTPA?si=652IBoYK7elQiH44
Tutorial to make Biofoam yarns: https://www.softrobotics.io/post/how-to-make-soft-biofoam-strings-exploring-an-affordable-and-accessible-fabrication-method